Tapflo UK is a well-established company specialising in the manufacture and supply of high-quality process pumps and bespoke solutions. At Tapflo UK, we supply a wide range of Diaphragm Pumps, Centrifugal Pumps, Peristaltic Pumps, Lobe Pumps as well as many other pump types suitable for a variety of applications.
Diaphragm Pumps are a foundation of various industries, recommended for their adaptability and dependability. However, even these pumps aren’t immune to operational hiccups that can disrupt their operation. Understanding these issues and their solutions is essential for safeguarding uninterrupted performance and efficiency within your process.
In this blog, we’ll look at common Diaphragm Pump issues, their causes and practical solutions to address these concerns.
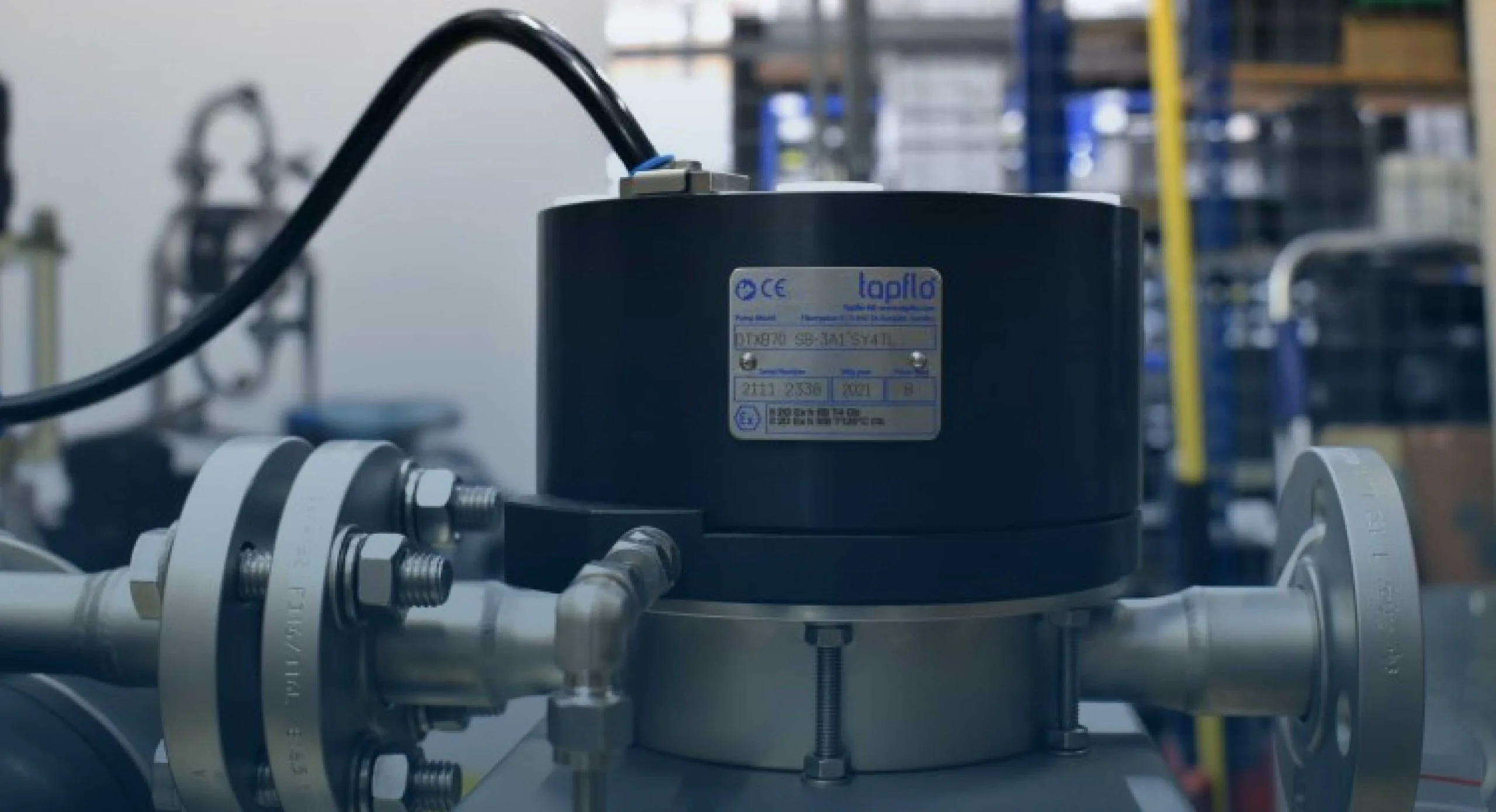
What is a Diaphragm Pump?
A Diaphragm Pump is a type of Positive Displacement Pump that uses two internal diaphragms that are commonly made from PTFE or rubber. These diaphragms work together to create pressure, pushing fluid through the pump. Inside the pump, the diaphragms control internal valves on the side, directing the flow of fluid and determining the amount transferred to the discharge outlet.
Tapflo UK’s Diaphragm Pumps are designed to be self-priming up to 5m from a dry suction pipe or 8m from a wetted pipe.
These pumps are highly effective across various industrial and Hygienic applications. They excel in pumping high volumes at low pressures and are robust enough to withstand diverse conditions.
Common Diaphragm Pump Issues
Your Pump Won’t Run:
Air Pressure Too Low
- Cause:Â The air supply pressure is below the required 1.2 bar or insufficient for the system pressure
- Solution: Increase air pressure using a filter-regulator. Ensure the mains air supply pressure meets the pump’s requirements
Blocked Air Connection or Contaminated Air Valve
- Cause:Â Air supply is obstructed or the air valve inside the pump is contaminated
- Solution: Check and clean the air supply, ensuring it’s free of obstructions. Inspect and clean the air valve
Blocked Muffler or Exhaust
- Cause: Impaired air expulsion affects the pump’s operation
- Solution: Check the pump’s exhaust for obstructions and ensure the muffler is in good condition
Solids in the Pump Chamber
- Cause:Â Solid particulates in the pump chamber block diaphragm movement
- Solution:Â Clean the pump thoroughly and install a suitable-sized filter on the suction to prevent blockages
Damaged Diaphragms or Ball Valves
- Cause:Â Wear, breakage or misshaping of diaphragms and ball valves
- Solution:Â Regularly check diaphragms and ball valves for damage and replace them as needed
Blocked Suction or Discharge Pipework
- Cause:Â Obstructed pipework prevents proper pump function
- Solution:Â Regularly check valve positions and clean pipework, especially when dealing with viscous or solids-laden fluids
Liquid is Leaking from Your Pump
Loose Side Housings
- Cause:Â Untightened tie rods lead to liquid leakage
- Solution:Â Ensure tie rods are tightened to recommended torque settings
Damaged O-Rings
- Cause:Â Perished or damaged O-rings on inlet or outlet manifolds
- Solution:Â Replace O-rings and ensure correct reassembly after maintenance
Diaphragm Rupture
- Cause:Â Overuse, abrasion, chemical attack or overpressure can lead to diaphragm failure
- Solution:Â Regularly check and replace diaphragms to prevent ruptures
Pipework Problems
- Cause:Â Mismatched pump and rigid pipework can cause leaks
- Solution:Â Match the pump to the installation, use flexible expansion bellows, hoses or a Pulsation Dampener to eliminate stresses
Worn or Blocked Valve Balls/Seats
- Cause:Â Impaired valve function leads to fluid circulation and syphoning
- Solution:Â Check and replace worn or blocked valve balls and seats
Air Leak or Changes to the Supply
- Cause:Â Changes in air supply quality, flow or pressure affect pump performance
- Solution:Â Regularly check for air leaks, changes in air supply and maintain air filter and moisture separators
Suction or Discharge Pressure Changes
- Cause:Â Encrusted or leaking pipework affects pump performance
- Solution:Â Routinely check connections, valves and pressure gauges to maintain system pressure
Blocked or Worn Air Valve or Muffler
- Cause:Â Damage, corrosion or dirt on the air valve affects pump function
- Solution:Â Monitor pump performance, conduct preventative maintenance and check the condition of the muffler
Understanding common issues associated with Diaphragm Pumps, identifying their causes and implementing our suggested solutions is key to ensuring optimal performance and longevity of your pump. Regular maintenance and proactive troubleshooting play a crucial role in maintaining an efficient and reliable system.
Read:Â Air-Operated Diaphragm Pump Troubleshooting Maintenance Guide
Maintenance Best Practices
Correct maintenance of your Diaphragm Pump is key to ensuring the longevity of your pump. Here are some essential maintenance tips to guarantee the extended lifespan and optimal performance of your Diaphragm Pump:
- Conduct routine visual inspections of the pump’s components, including diaphragms, valve balls, seats and connections, to identify signs of wear or damage
- Check and tighten the pump’s main nuts and bolts to the specified torque settings. This reduces the risk of leaks and ensures the pump’s integrity
- Monitor and clean/replace the air filter regularly to ensure the quality of the compressed air supplied to the pump. Contaminated air can lead to O-ring rupture and pump stalling
- Keep the air exhaust muffler clear of any obstructions as a blocked muffler could affect the pump’s ability to expel air efficiently
- During maintenance checks, inspect diaphragms for signs of wear, reducing the risk of diaphragm rupture
- Check valve balls and seats for wear or damage and replace any worn/broken components to maintain valve function, preventing fluid circulation inside the pump
- Regularly inspect suction and discharge pipework for blockages or leaks. Proper valve positioning and cleaning of pipework are essential, especially for fluids with solids
- Ensure there are no air leaks in the system. Changes in the quality, flow or pressure of the air supply can directly impact pump performance
- Routinely monitor suction and discharge pressure gauges to ensure the system pressure remains within the working parameters of the pump
- Mount the pump correctly on a solid surface with anti-vibration feet. Use wall or floor mounting brackets with anti-vibration feet to minimise vibrations and stress on pump components
- Use a level control system to monitor media levels on the suction or discharge. This ensures the pump is turned off when levels reach set points, preventing dry running
- Train operators on correct pump usage and maintenance procedures. Emphasise the importance of following recommended schedules for servicing and part replacement
Ensure the compatibility of the pumped media with the pump’s construction materials. Use compatibility charts, such as the Cole Palmer Compatibility Guide, and consult manufacturer guidelines for correct material selection
Tapflo UK's Recommendation
Metal Barrier Diaphragm Pump
Consider a Barrier Pump for added protection in the event of diaphragm rupture. Barrier Pumps feature backup diaphragms for fluid containment during failures.
Diaphragm Pump Guardian System
Additionally, a Guardian System can be used to monitor fluid discharge pressure, preventing dry running and providing added protection in deadhead, stop/restart and barrier situations. Another way to avoid dry running is to use a level control, which can also be purchased from Tapflo UK and will work with any Diaphragm Pump.
Conclusion
To summarise, keeping your Diaphragm Pump in optimal working condition allows you to promptly deal with any issues that arise. Whether its maintaining air pressure or conducting regular check-ups, taking proactive care ensures your pumps last longer. Tapflo UK is committed to offering complete fluid handling solutions, helping operators tackle and avoid challenges in their Diaphragm Pump system.