When looking for a pump that can work for almost any of your requirements, the popular diaphragm pump is a great option to consider for your application. Here at Tapflo UK, our range of Air Operated Diaphragm Pumps are renowned for being an extremely versatile option for many different fluid viscosities, flow rates, air pressures and temperatures. By understanding the correct way to install a pump for your requirements will help to greatly improve the long life of the pump and minimise downtime. So what are the different type of installations available and how do you install a diaphragm pump?
Types of Installations
The type of installation you require will be dependable on the application being pumped.
The Tapflo Air Operated Diaphragm Pump is flexible to many types of installations. Furthermore, as the inlet and outlet ports can be rotated through 180º piping systems, this reduces the work of the pump and the installer! Below are 3 types of installations in which Tapflo Diaphragm Pumps can be operated in:
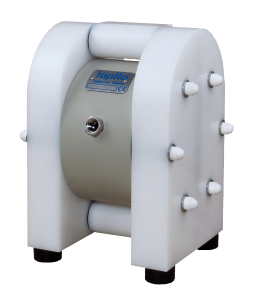
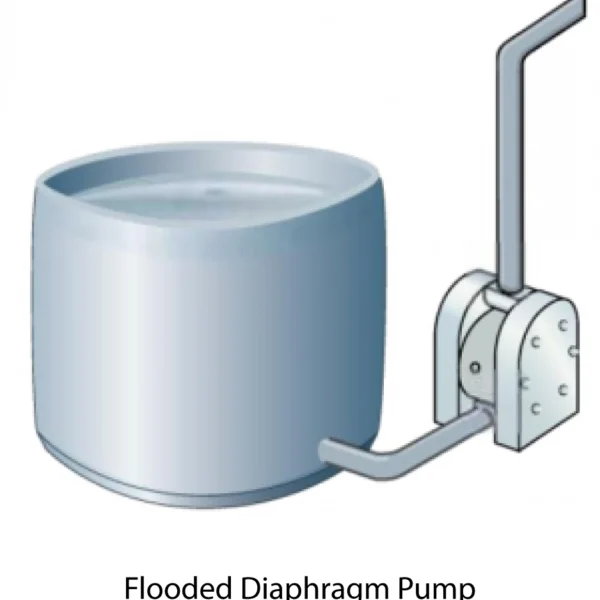
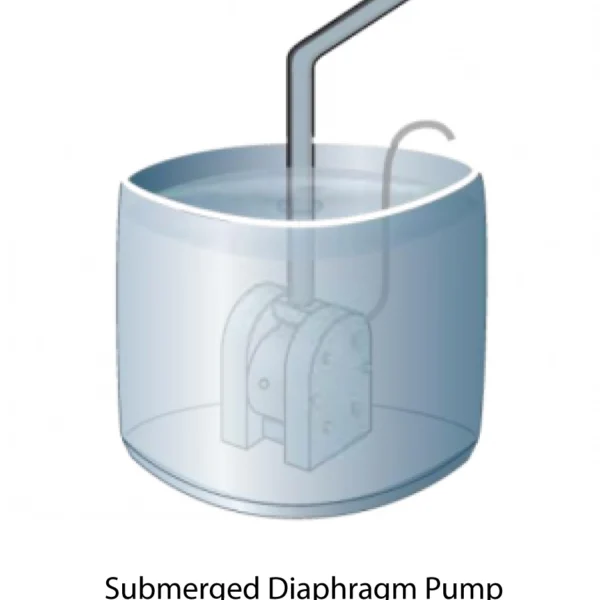
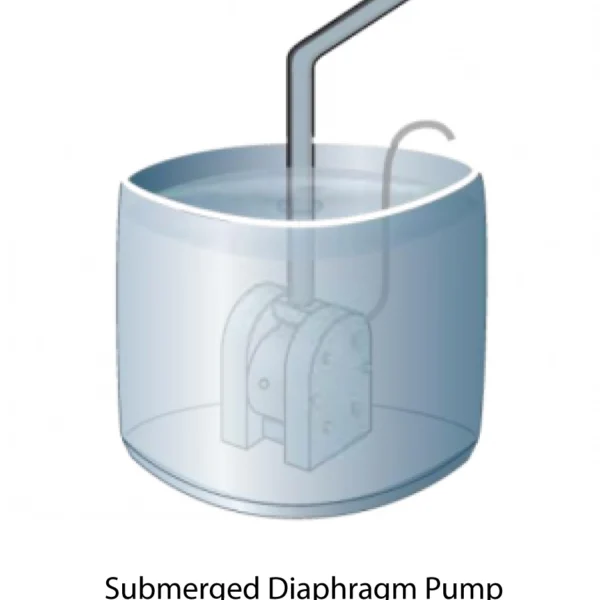
Trolley Mounted
Another great install option, especially for the chemical industry, is for your Air Operated Diaphragm Pump to be on a mobile decanting unit. This includes a Pneumatic Batcher, PoD Valve (Point of Dispense) and the diaphragm pump all mounted onto one of Tapflo’s bespoke trolley unit’s. These are designed and manufactured in house to suit each clients requirements and can accommodate 20L, 25L or 205L chemical containers. This option is ideal for chemical transfer applications to reduce the risk of carrying containers to different areas of your factory operations. If you would like to find out more about our trolley mounting options, take a look at our mobile decanting unit page.
Floor or Wall-Mounted
Tapflo’s stationary decanting system allows for a diaphragm pump to be installed either floor-mounted, where the upstand with the pump and batcher are all mounted within, or wall-mounted, with the pump and air preparation mounted on a wall bracket. The wall-mounted option is can be an advantage especially when there is limited space available on the factory floor.
How to install a Tapflo Diaphragm Pump
Below is an installation example, showing best practice when installing a Tapflo Air Operated Diaphragm Pump. Please note, our air valves are constructed for oil-free air, lubricated air is not permitted and will damage the pump. However, if the air is very dry (laboratory air), the air may be lubricated with water. The maximum allowed air pressure is 8 bar, and as a preventative measure, the air must be filtered to at least 5 microns or less. The recommended air quality according to PN-ISO8573-1:2010 is particles class 6, water class 7 and oil class 4.
To facilitate the operation of the pump, and cater for the above parameters, we recommend an air treatment system connected to the air supply.
These components should be included:
- Regulator to adjust the air pressure and therefore the discharge pressure generated by the pump.
- Manometer to read the output pressure to the pump
- Needle valve to adjust the airflow to the pump and therefore the flow rate generated by the pump. This is especially useful when operating the pump in the lower ranges of its performance capabilities and for accurate control of flow rate.
- Filter to ensure that the pumps air valve doesn’t become contaminated.
The following components are included in Tapflo’s Air treatment system which can be ordered from us and installed onto the pump so that it is ready to use upon delivery.
- Gate valve for isolating compressed air supply
- Air Filter and Pressure Regulator w/ mounted Manometer
- Flexible Air Hose feeding to the pump Air Inlet
- Needle Valve for regulating the pump’s flow rate
- Flexible Suction Hose feeding to pump suction side to absorb any vibrations and water hammer effects.
- Gate Valve fitted to the pump suction to enable insolation for maintenance.
- Gate Valve fitted to the pump discharge to enable insolation for maintenance.
- Coiled flexible piping fitted to the pump discharge to provide back pressure and also the required distance between the pump and flow gauge/meter to retain accuracy.
- Flow gauge to provide an accurate readout of generated flow to ensure that the pump is working comfortably.
Note: Isolation valves can be fitted to the pump ports using unions and flexible hose attached to fluid components by means of hose tails and hose clamps/jubilee clips.