As a leading UK-based manufacturer of process pumps and fully integrated systems, Tapflo UK was approached by a market-leading provider of all trade and construction products for Builders’ Merchants and Trade Professionals. The client required a reliable, safe, and automated system to manage the offloading and distribution of various liquid catalysts from IBCs (Intermediate Bulk Containers) to 12 separate production lines, each with its own local storage tank.
Faced with growing production complexities, manual handling inefficiencies, and strict safety standards, the client needed an engineered system that would enhance operational control, minimise risk, and provide live monitoring of chemical stock levels. As specialists in hygienic, low-energy pumping technologies and bespoke control automation, Tapflo UK was uniquely positioned to design and deliver a turnkey solution.
Application Details: The Client's Challenge
Our client’s existing approach to catalyst offloading and distribution was labour-intensive and risk-prone, relying on manual connection and transfer from IBCs to multiple production lines. Several core issues were identified:
- Lack of automated level monitoring, leading to unexpected product shortages or overfills
- No integrated pump control, increasing operator dependency and inconsistent flow management
- Risk of catalyst spillage or incorrect dosing due to manual valve actuation and pump triggering
- Energy inefficiency and unreliable performance from legacy Diaphragm Pumps in similar applications
- Poor visibility of IBC fluid levels across the plant floor and no remote access to status or diagnostics
These challenges led to production delays, unnecessary downtime, and safety concerns around catalyst handling.
System Components: Our Engineered Solution
We provided a fully integrated catalyst offloading system incorporating IBC level monitoring, automated pump and valve actuation, and centralised control via a bespoke PLC-based control panel.
Pumping Technology:
6 x Tapflo TC225 STT-11SFRMV Sanitary Air Operated Diaphragm Pumps with integrated LEAP (Low Energy Air Pump) Technology:
- Wetted parts: AISI 316L Stainless Steel, PTFE TFM diaphragms and seals
- Max capacity: 330 L/min; Max pressure: 8 bar
- Tri-Clamp inlet/outlet connections for hygienic transfer
- Fitted on 3 x dual stainless steel skids with integral drip trays and built-on air treatment systems (regulator, filter, needle valve, isolation)
LEAP Technology Highlights:
- Ultra-low start pressure (0.2 bar)
- Energy savings up to 70%
- Built-in stroke monitoring for batch accuracy
- Stall-free operation and reduced pulsatio
- Simple integration via 24VDC control signal and dry contact feedback.
Level Monitoring System:
6 x VEGAPULS C 21 Radar Sensors mounted above IBCs using a bespoke aluminium extrusion framework:
- 80GHz non-contact radar for high accuracy (+/- 5mm)
- Bluetooth enabled for live monitoring and diagnostics on mobile/tablet (25m range)
- Connected to PLC to trigger pump stop when IBC levels fall below 5%
Control & Automation:
1 x Custom Control Panel with Siemens S7-1200 PLC and safety relay:
- Monitors catalyst requests from 12 production lines
- Controls 6 pumps and up to 16 solenoid valves
- Interfaces with existing production PLCs to manage catalyst delivery logic and safety protocols
Control Features:
- Low-level shutoff and indicator LEDs
- Stroke-counting logic to prevent over-dosing (e.g., stops at 500 strokes)
- Pump fault alarms (no stroke detection)
- Re-request protocol after IBC replacement to avoid unintentional restarts
Valves & Fittings:
16 x Sanitary 3-Piece Ball Valves with Valbia SR075 pneumatic actuators, 24VDC solenoids, and switch boxes for open/closed feedback:
- Hygienic connections using IBC Buttress to Tri-Clamp adaptors (PP and AISI 316), or PTFE Tri-Clamp seals for chemical resistance
- All valves and fittings were selected for FDA/3A compliance and corrosion resistance
Additional Safety & Bunding:
- 3 x Double IBC Bund Pallets (1350L capacity each), UV-stabilised polyethylene, PPG26 compliant
- Free 75L spill tray for minor handling operations
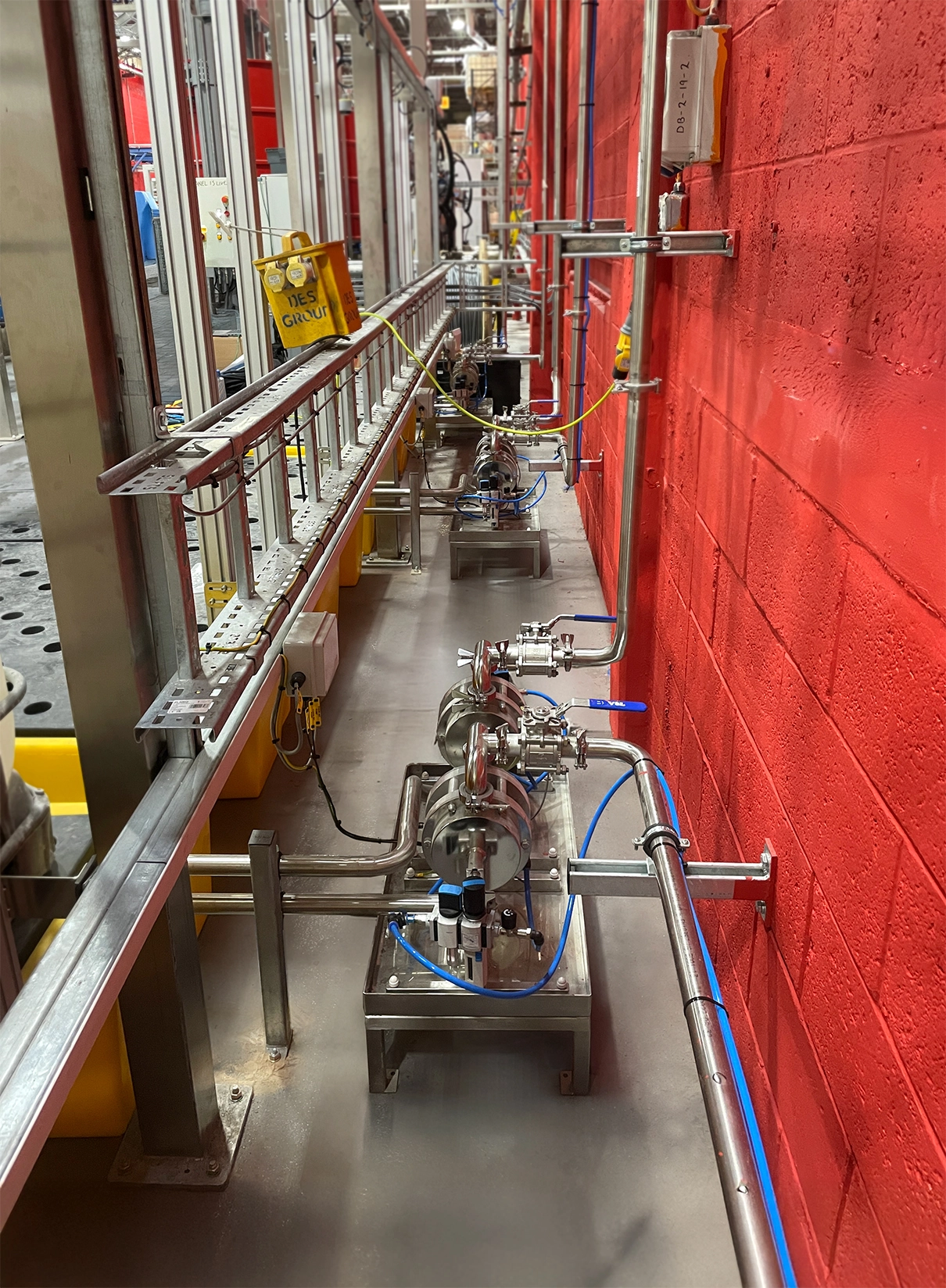
Benefits of The Solution
Our system delivered a fully automated, hygienic, and energy-efficient solution that eliminated manual handling, reduced operating costs, and greatly improved control and visibility. Key benefits included:
- Automated, accurate catalyst delivery to 12 production lines with no manual intervention
- Live level monitoring via Bluetooth ensures real-time visibility and proactive refill scheduling
- Improved safety through low-level lockout, stroke count limits, and fault alarms
- Energy savings up to 70% using LEAP technology – significant annual OPEX reduction
- Hygienic, stainless-steel system with Tri-Clamp connections and sanitary valve packages
- Fully integrated PLC control providing seamless interfacing with existing factory systems
- Modular skids allow simple relocation and maintenance
- Minimised downtime with fast air valve serviceability (under 2 minutes)
- No pulsation dampeners required, thanks to reduced pulsation from LEAP pumps
While demonstrating our technical capabilities, this project also highlighted our commitment to designing and delivering engineered systems that seamlessly integrate into complex manufacturing environments. By understanding the client’s unique challenges, from precise catalyst delivery to production-line responsiveness, we delivered a solution that was scalable, reliable, and efficient.
This project is a perfect example of how smart integration between advanced pumping technologies and intelligent control systems can drive production efficiency, improve safety and reduce operational overheads.
Ready to transform your fluid handling process?
Whether you’re looking to improve process control, reduce energy usage, or integrate smart system automation, our team is ready to help you design a solution that fits your operational requirements.
Get in touch with Tapflo UK today, and our engineers will be happy to discuss your process challenges.
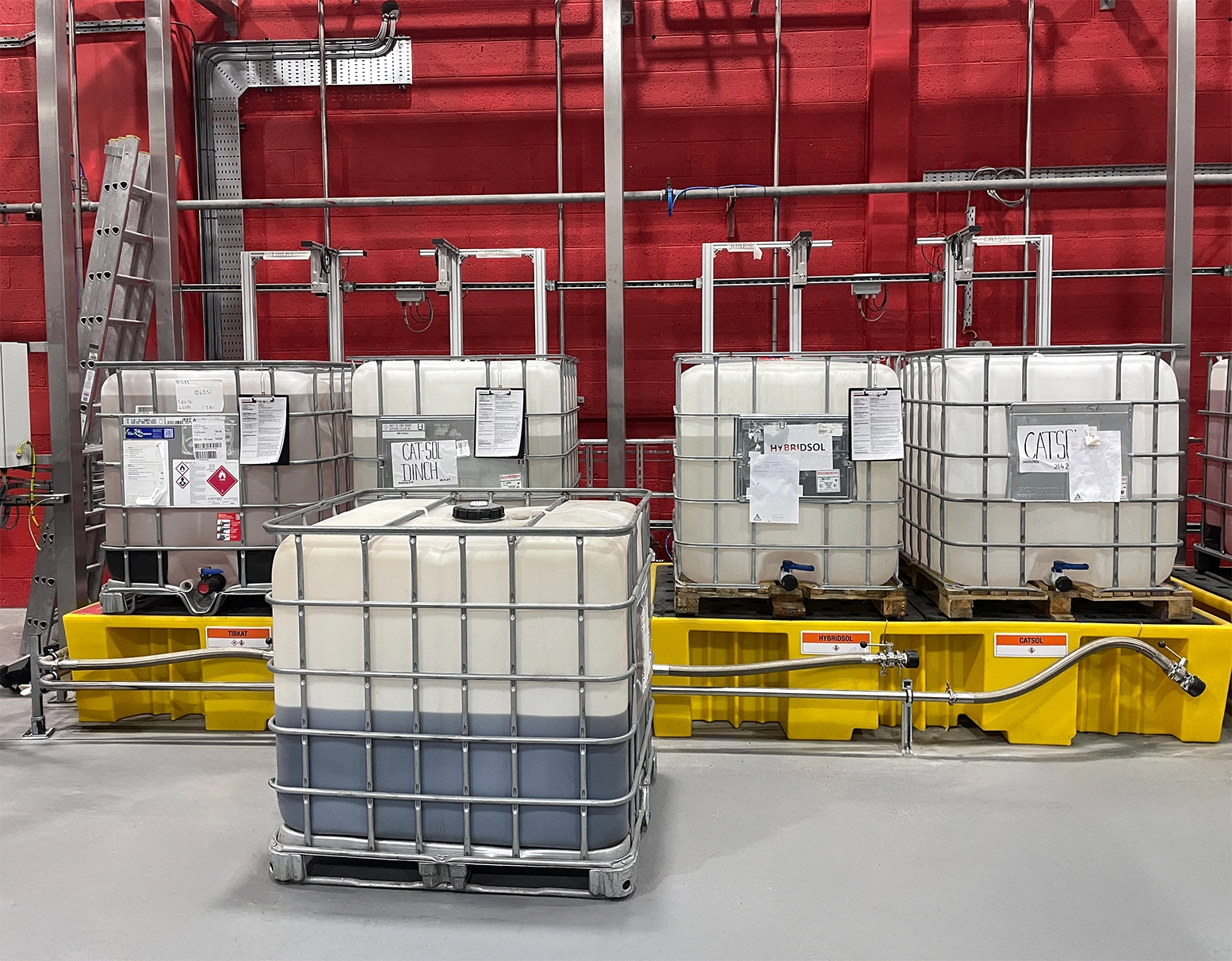