Our client, a leading industrial cleaning and maintenance contractor, approached us as they were looking for a robust, safe and efficient solution to handling high-volume, chemically aggressive waste effluent that was being generated onsite during cleaning operations. Having previously relied on an open IBC storage that required manual operation, the facility faced serious environmental compliance and Health and Safety (H&S) risks, including frequent spillage, inefficient operator response, and insufficient containment infrastructure.
To address these challenges, our multi-disciplinary engineering team designed and deployed a semi-automatic bunded waste handling system uniquely tailored to their specific operational and compliance requirements.
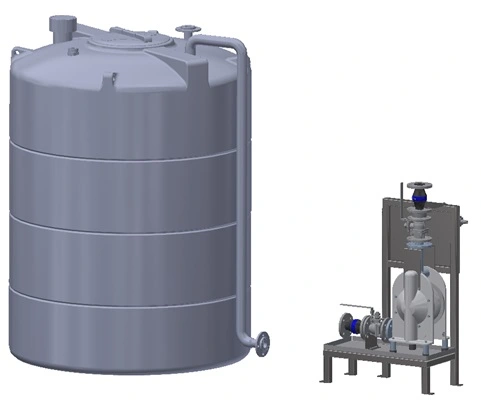
Application Details - The Challenge
The facility’s primary challenge was to safely contain, monitor and discharge varying volumes of chemically aggressive waste effluent that often contained solids and detergent residues. Specific operational pain points included:
- Spillage risks during uncontrolled inflow (overflow can occur if inflow isn’t shut off in time)
- Inefficient manual monitoring and response (operators may miss critical level limits without real-time alerts or controls)
- Inflexible Fill/Empty levels (static level settings don’t accommodate day-to-day volume fluctuations)
- Hazardous material exposure to operators and the environment (manual operation requires operators to work near potentially dangerous fluids)
- High cost of civil bunding (traditional bund construction is expensive and time-consuming)
System Components - Our Solution
To overcome these challenges, our team designed and implemented a 1500L Semi-Automatic Bunded Tank Emptying System, which included:
Storage & Containment
1500L Bunded HDPE Tank:
- Closed-top, flat-bottomed, rust-proof design
- 110% integrated bund capacity for full environmental compliance
- 4” mushroom vent, removable lid, and multiple inlet/outlet connections
- No low-level fittings ensure over-the-top fluid entry and exit
Fluid Handling & Transfer
1½” Air-Operated Diaphragm Pump (AODD):
- Aluminium construction for chemical compatibility (PTFE and Stainless Steel AISI 316L available)
- Solids-handling capability up to 10 mm in diameter
- Mounted to bespoke Stainless Steel AISI 316L drip tray with expansion joints and isolation valves
- Manual control via 6-200-003FX Air Treatment & Control Set (upgradeable to 6-200-005FX for full automation)
Level Control & Automation
VEGAPULS C22 Radar Level Sensor:
- Non-contact 80GHz radar technology
- ±2 mm accuracy with 15m range
- Bluetooth-enabled for wireless monitoring and parameter adjustment
VEGAMET 841 Level Display & Controller:
- Visual LED indication (green for ‘full’, red for ‘empty’)
- Infinitely adjustable setpoints for flexible fill/empty thresholds
- Bluetooth-compatible for remote diagnostics and control
Operator Interface
Forward-facing Control Stand with:
- Manual air treatment controls
- VEGAMET display for immediate visual feedback
- Clean, ergonomic layout for safe and intuitive use
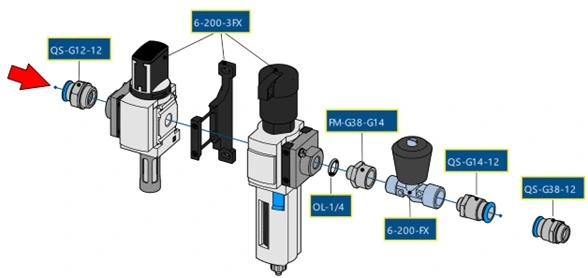
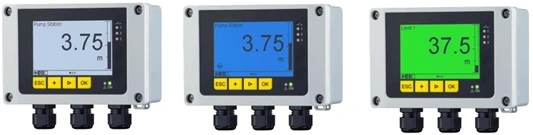
Benefits of the Solution
- Spill-Free Operation: Automated valve control linked to the radar sensor ensures effluent intake stops precisely at the designated fill level, removing spillages and reducing health and safety risks
- Enhanced Operator Safety: The fully bunded, sealed system eliminates open storage and manual handling requirements, significantly reducing the risk of contact with hazardous fluids
- Flexible Performance: Bluetooth-enabled VEGAPULS and VEGAMET technologies allow remote access for diagnostics, live tank level monitoring, and spontaneous setpoint adjustments
- Manual or Automated Emptying: Operators now initiate discharge based on real-time display feedback. The system is upgrade-ready for full automation via the optional 6-200-005FX kit
- No Civil Bund Required: With a 110% containment bund integrated into the tank design, the need for costly and space-consuming civil bund construction is reduced
- Scalable and Serviceable: The modular design and chemically resistant components allow for easy maintenance and future scalability, supported by a 10-year tank and 5-year pump warranty
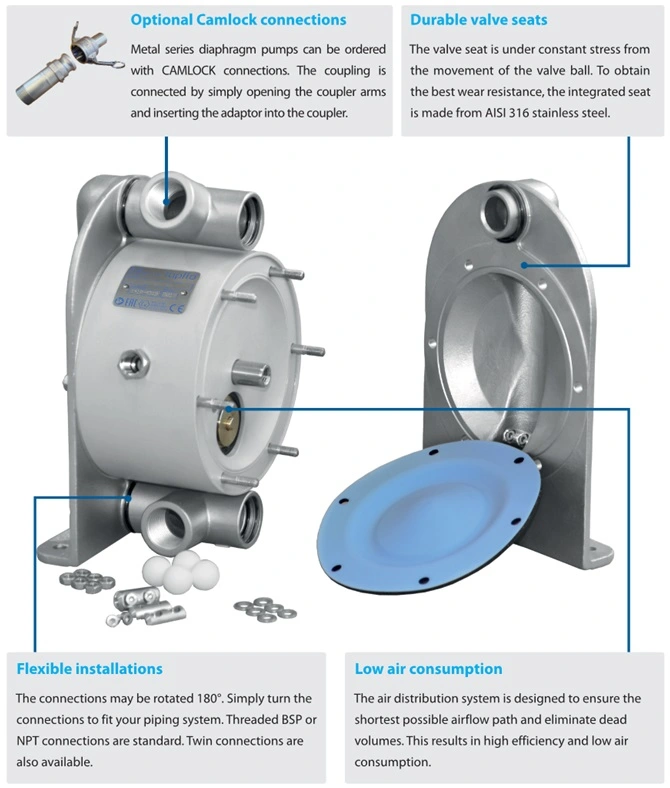
Ready to transform your fluid handling process?
The implementation of this Bunded Tank System has transformed waste effluent handling at our client’s facility. The semi-automated, sensor-driven approach ensures compliance, enhances operator safety, and introduces flexibility and scalability to meet the evolving operational requirements of the site. With plans to integrate full automation via the 6-200-005FX module, this system not only solves their challenges today but also supports scalability in their facility.
Are you looking for a similar solution? Does your facility handle highly corrosive and aggressive media? Talk to our team for a solution tailored to you.